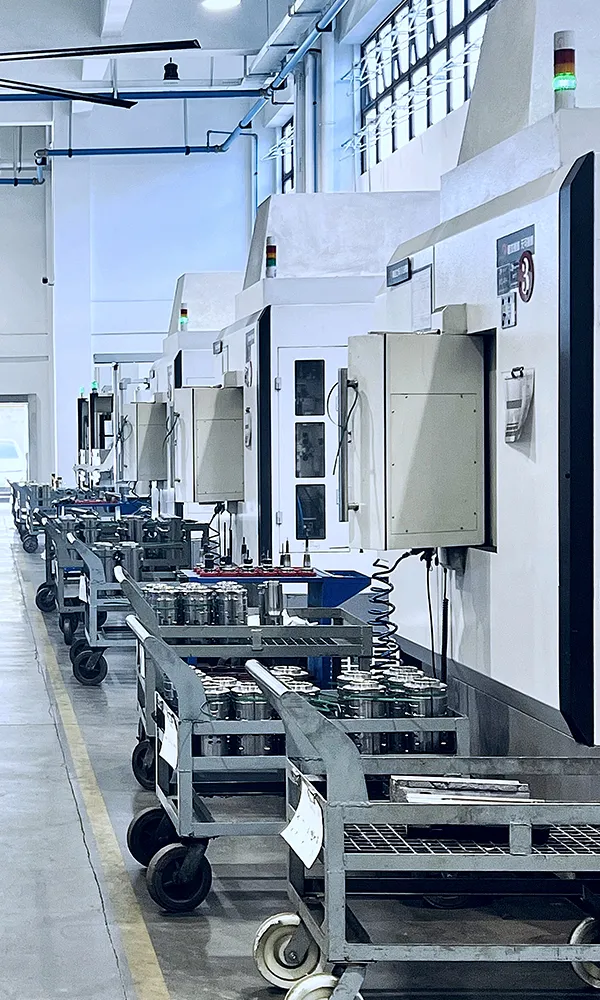
نظام FMS: تعزيز الكفاءة في تصنيع قوالب تشكيل الزجاجات
من خلال دمج خط إنتاج متطور بنظام سي إن سي مستورد من أوروبا، نجحنا في تعزيز كفاءة الإنتاج وضمان التسليم السريع للقوالب عالية الجودة.
- واجهنا التحدي
في عام 2016، أعرب أحد العملاء الأوروبيين منذ فترة طويلة عن حاجته إلى منتجات لكن شرط أن يكون زمن التسليم أسرع وجودة المنتج من القوالب تكون بأعلى المعايير لتلبية متطلبات السوق المتزايدة. - الحل
لتلبية هذه المتطلبات، بدأت شركتنا ORI Mould سلسلة من التحديثات في عام 2017، حيث أدخلت مراكز تصنيع أفقية مخصصة ودمجها مع خطوط إنتاج مرنة متقدمة تم استيرادها من أوروبا. وقد تضمنت هذه الأنظمة الجديدة أجهزة الكشف الأوتوماتيكية وأنظمة تحديد الأدوات، مما أدى إلى تحسين دقة تحديد مواقع القوالب بشكل كبير. ولتحسين كفاءة الإنتاج بشكل أكبر، قامت الشركة بتركيب نظام 78 منصة، مما أتاح التبديل الآلي الكامل للإنتاج على مدار 24 ساعة، إلى جانب نظام جدولة متقدم يحدد أولويات مهام الإنتاج بشكل ديناميكي. وقد سمحت هذه الابتكارات بعمليات تصنيع المنتجات على مدار 24 ساعة طوال أيام الأسبوع دون انقطاع. - تحقيق النتائج
حققت التحديثات نتائج ملحوظة، حيث تم تقليل أوقات التسليم، مما أتاح تسريع الإنتاج لمدة 15 يومًا للطلبات العاجلة، بينما زادت الطاقة الإنتاجية الشهرية لخط التصنيع الذكي وحده إلى 5,000 قالب فارغ بالنفخ. وعلاوة على ذلك، أدت التحسينات كذلك إلى تحسينات كبيرة في جودة القوالب، وقد أشاد بنا العميل وأثنى علينا ثناءً كبيرًا. وقد عزز هذا التعاون الناجح الشراكة طويلة الأمد، والتي لا تزال تزدهر حتى يومنا هذا.
تسلط هذه الحالة الضوء على التزامنا بتلبية احتياجات ومتطلبات العملاء من خلال الابتكار والكفاءة والموثوقية.
تطوير تكنولوجيا اللحام في شركة ORI Mould
على مر السنين، قامت شركتنا بصقل تكنولوجيا اللحام الخاصة بها، والانتقال من الأساليب التقليدية إلى الحلول المبتكرة لمواجهة تحديات الإنتاج وتلبية متطلبات الصناعة المتطورة.
- المرحلة الأولى: اللحام اليدوي التقليدي باللهب اليدوي
قبل عام 2008، اعتمدت الشركة على اللحام اليدوي التقليدي باللهب. وفي حين أن هذه الطريقة وفرت طبقات لحام موحدة وكانت مناسبة تمامًا للتطبيقات التقليدية، إلا أنها كشفت عن قيود كبيرة مع نمو حجم الإنتاج. وقد جعل التشغيل اليدوي من الصعب الحفاظ على الاتساق في التصنيع على نطاق واسع، مما أدى إلى مخاطر مثل انفصال طبقات اللحام وعدم اتساق الجودة التي شكلت تحديات للإنتاج الفعال. - المرحلة الثانية: اللحام بالقوس المنقول بالبلازما (PTA)
للتغلب على قيود اللحام اليدوي، اعتمدت الشركة تقنية اللحام بالقوس المنقول بالبلازما (PTA) في عام 2009. وقد أدى هذا التحديث إلى تعزيز قوة الوصلات الملحومة بشكل كبير. ومع ذلك، أدخلت تقنية اللحام بالقوس المنقول بالبلازما تحديات خاصة بها، بما في ذلك التأثير الحراري العالي على المواد الأساسية وصعوبات في التحكم في معدلات التخفيف. وقد أدت هذه العوامل في بعض الأحيان إلى طبقات لحام غير متساوية وتقلبات في الجودة. - المرحلة الثالثة: التكسية بالليزر
بعد ثماني سنوات من البحث المشترك مع الشركاء، انتقلت الشركة إلى تقنية التكسية بالليزر في عام 2019. وتجمع هذه الطريقة المتقدمة بين دقة اللحام اليدوي وكفاءة اللحام بالليزر. كما تسمح الكسوة بالليزر بالتحكم الدقيق في أبعاد طبقة اللحام وتوفر سرعات لحام أسرع، مما يجعلها مناسبة بشكل خاص لتطبيقات الضغط والنفخ ذات العنق الضيق (NNPB) وخطوط الإنتاج عالية السرعة. كما أنها تحسن بشكل كبير من الجودة الجمالية لأسطح الزجاجات، خاصةً عند اللحامات. وباعتبارها تقنية لحام على البارد، فإن الكسوة بالليزر تقلل من الأضرار الحرارية، مما يمكننا من تلبية جداول التسليم ومعايير الجودة الصارمة بشكل متزايد في الصناعة. ومن خلال هذه التطورات، أظهرت الشركة التزامها بالابتكار والتميز، مما يضمن بقاء تقنيات اللحام الخاصة بها في طليعة صناعة تصنيع القوالب المخصصة لتشكيل الزجاجات.